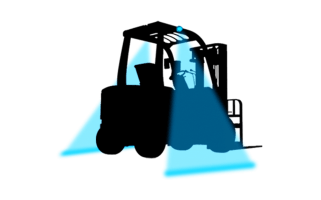
6 Essential Devices That Ensure Forklift Safety
Forklifts are essential in a warehouse setting for handling heavy loads. However, these pose a significant danger to operators, pedestrians, structure, and products. business owners have a huge task of encouraging safety in the workplace at all costs. Additionally, ensuring safety meets Occupational Safety and Health Administration (OSHA) standard in the workplace. Here are essential safety devices on a forklift that require appropriate maintenance to avoid injury and damage.
1. Brakes
These are obviously the most important safety features on any motorized vehicle. Malfunctioning brakes make workplace accidents inevitable. Operators have to inspect the brakes fully before each shift. This allows testing the functionality of brakes and brake lights. Malfunctioning brakes, brake lights, and brake pads make the forklift not good for use. Using the forklift again requires applying appropriate repairs before a full inspection to ensure it passes safety standards. Some of the bad habits that encourage brake failure include:
- Driving with engaged parking brakes
- Regular quick or sudden stopping
- Driving too hard
- Braking aggressively during operation
- Damage to wheel cylinder and hub seals
2. Lights
In a warehouse setting, lights alert other operators and workers about an approaching forklift. Lights are very important since drivers usually focus on the truck front. This makes investing in forklift blue safety lights essential for safe operation. A forklift needs headlights, taillights, and backup lights for safety. These lights need prompt replacement when they develop defects. Forklift lights communicate essential messages to others in the workplace.
Red zone lights are easy for other workers to spot to limit accidents and injuries. Forklift blue light allowing everyone knowing that there is a forklift coming. These lights are great for nighttime duty, fog, and in dimly lit indoor places. Top-mounted warning lights offer bright illumination for safety in a distribution center, warehouse, or other job sites that require a forklift.
3. Overhead guards
These protect operators from falling items but can’t hold up full load falls. The operator should wear a hard hat and other necessary protective wear. Regular use of a forklift of poor maintenance encourages missing bolts, broken welds, dents, and other forms of damage. Periodic inspection is required to fix these and ensure workplace safety. Replacement of overhead guards is necessary to limit safety concerns.
4. Seatbelts
Forklifts come with a restraint system for operator protection. Seat belts keep operators safe during a tip over. The operator stays inside the forklift using a seatbelt while holding on tight and leaning away from the point of impact. Regular inspection and repair are very important to ensure that the seatbelts are always in good condition to keep operators safe.
Common accidents during forklift operation result from overturning. This comes with injuries and deaths in severe cases. The seatbelt keeps the operator safe in the cabin. With the seatbelt on, the operator can’t jump out and fall underneath the forklift.
How to stay safe during a forklift turnover
- Keep the seatbelt well adjusted
- Push hard against the steering
- Brace feet firmly on the floorboard
- Place both hands on the steering leaning forward
- Leaning away from the impact point
5. Horn
A broken or damaged forklift horn puts everyone including the operator and pedestrians in your workplace. Accidents resulting from a malfunctioning horn puts your business at risk of battling negligence suits in court. Before and after every shift, checking the condition of the forklift horn is very important. The horn is an essential aspect of forklift operation and honking it is an essential safety measure. Encourage operators to report when their horns are malfunctioning or missing.
Horns are mechanical devices prone to regular wear and tear from frequent use. This makes them wear out much faster than other parts on a forklift. Competent fleet maintenance personnel should replace any malfunctioning horns. Using a forklift with a broken horn is dangerous as driving without steering or brakes.
6. Rearview mirrors
Adding right or left mirrors enhance workplace safety when using a forklift. These mirrors allow visibility of the rearview limiting chances of accidents. Operators can easily look into and see 150 degrees behind the forklift. It is possible to perceive everything behind the right and left hand shoulder but mirrors make this easier.
Rearview mirrors have no blind spots and offer a much wider view of the forklift rear. A truck with wide-angled mirrors gives the operator better view of the rear to limit collisions. Installing forklift mirrors lessens physical strain on the operator’s head and neck. These encourage less turning to see all angle directions during reversing.
Conclusion
Keeping these essential safety devices in order backed by others like wearing protective gear ensures a safer workplace. Maintaining these devices makes accidents and injuries less likely to happen. Fitting blue safety lights on the forklift makes it easy to notice an oncoming truck. Additionally, the light makes the path well illuminated to avoid damage to structures and items.