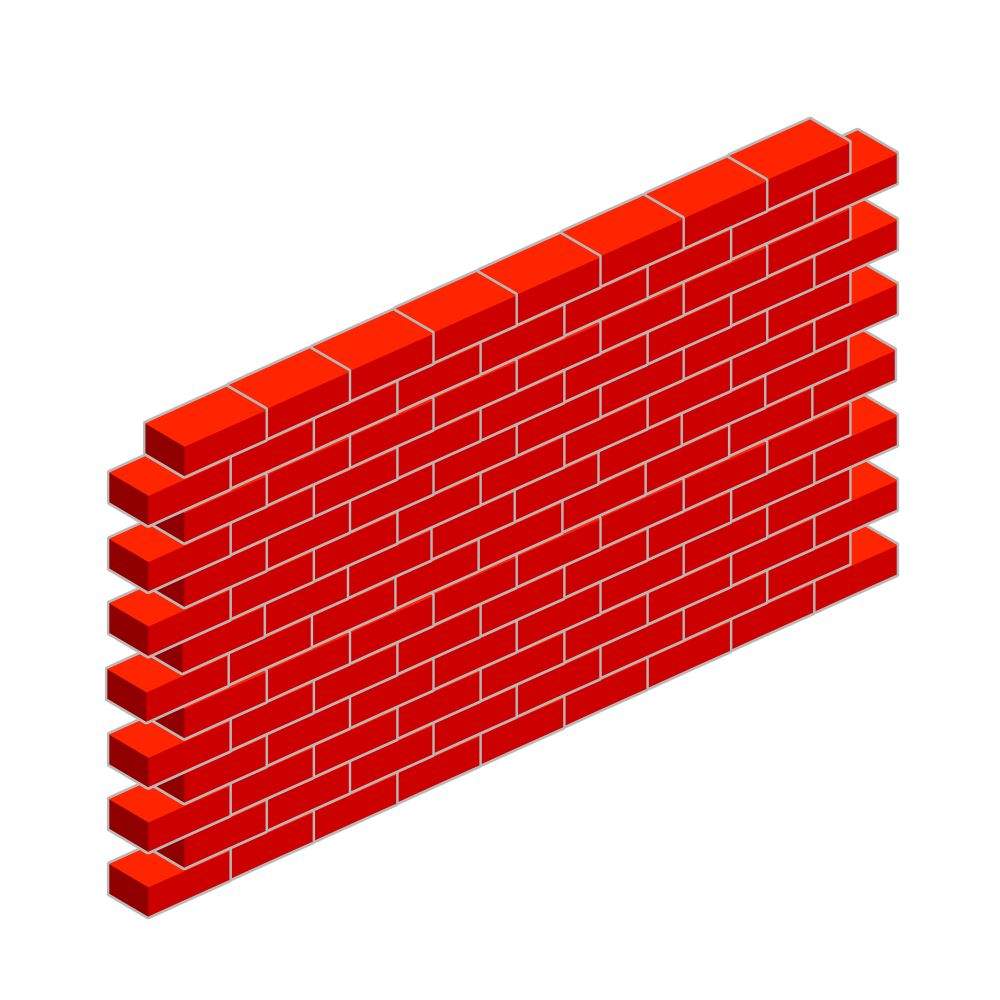
The 9 Biggest Mistakes When Building Your Facade
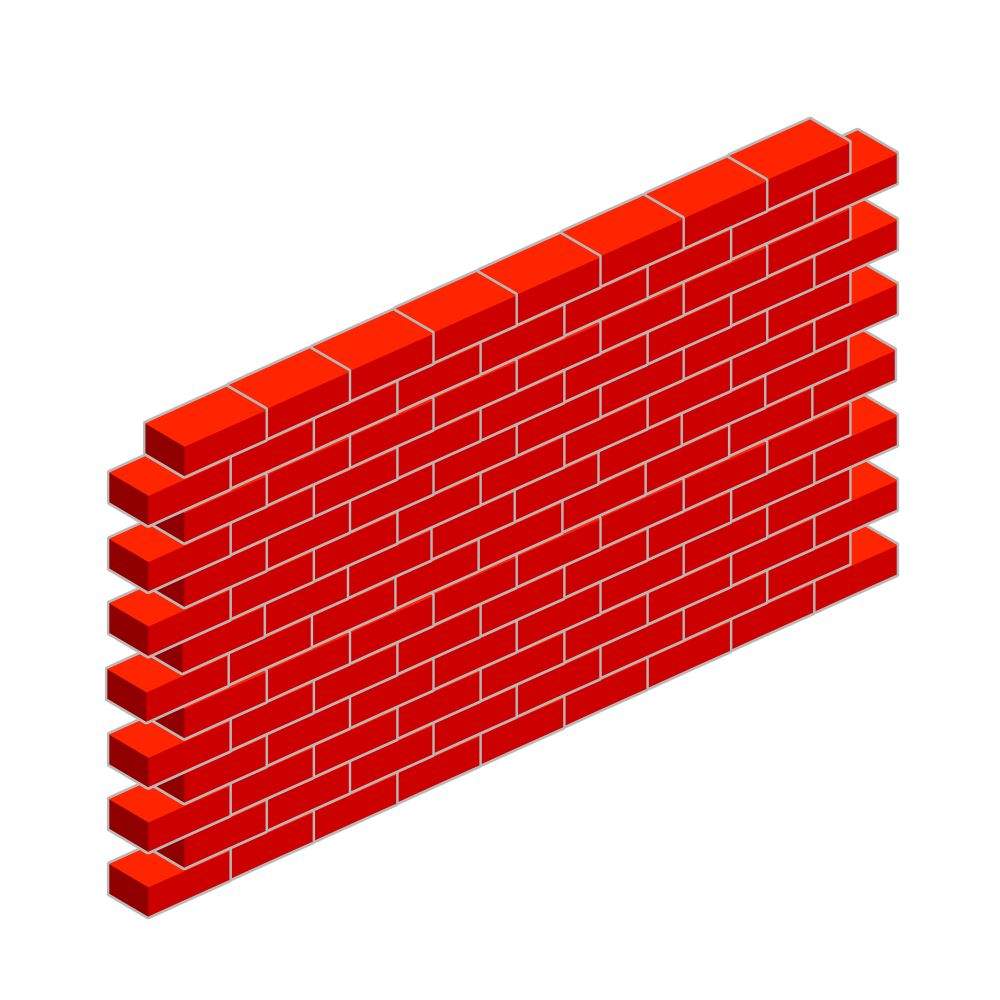
Despite the many alternatives, the average builder still swears by the brick to finish his facade. An important condition for a good end result is correct processing. Many home builders and some contractors make mistakes here. Livio’s asked brick manufacturer to list the most commonly made mason sins.
1: Not having an eye for detail
The choice of our facing bricks often reflects our personality. Your façade masonry must, therefore, look beautiful, now and in the future. In addition to making the right choice, it is of course also crucial to process everything correctly. In addition to the traditional bricklaying of the facing bricks (joint thickness 10-15mm), you can also apply other techniques, such as bonding and thin bricklaying (joint thickness 5-8mm).
Choice and processing of the facing brick
But which stone should you choose now? In any case, choose a facing brick with a BENOR quality mark, then you are assured of quality. This quality label proves that an external independent check has been carried out on the various facing brick properties.
For rustic stones, choose tumbled stones instead of the real recovery stones. Tumbled stones have a quality base stone, which was produced under controlled conditions. When using real recuperation bricks, harder and softer fired bricks are all too often combined during processing, with the risk of frost damage.
Important! A ceramic facing brick consists of the natural elements water-air-clay-fire. This creates small mutual color differences between the different packages. That is why you should never process a pallet per pallet, but at the same time, you take stones diagonally from 4 to 5 packs. This prevents striking color delineations in the facade.
2: Mortar not aligned with the brick
Each brick can absorb less or more water in a given time than any other brick. If the mortar is not adapted to the suction behavior of the stone, you risk structural and aesthetic damage. In case the stone absorbs the mixing water too quickly, the mortar ‘burns’ with pulverization and poor adhesion as a result.
If you work with a weakly absorbent type of stone, the stones can start to ‘float’.
Conclusion: make sure you choose the right mortar type. The suction behavior of the stones is indicated on the packaging or the technical data sheet as under the heading ‘initial water absorption’.
3: Incorrect preparation of the laying and grouting mortar
The choice of ingredients for the preparation of the mortar is extremely important. Contaminated water, the wrong type of sand, an incorrect quantity, the cement type, the addition of unsuitable additives (e.g. dishwashing detergents) are – just like incorrect mixing ratios – not allowed. This can result in the ‘floating’ of the stones, in a reduced compressive and adhesive strength of the mortar, and invisible contamination of the stone.
In the case of colored joints, it is best to choose inert color pigments. These provide a coloring in the mass and do not react with other substances. That way you avoid color differences and leaching.
It is therefore recommended to work with ready-made factory mortar as much as possible. You only need to add water to this. There are many types of mortar whose color and properties are adapted to the facing brick, the type of processing, and the processing conditions.
4: Poor detailing of the facade
Keep in mind that some special detailing involves risks for pollution. Take the necessary measures in consultation with the architect. Attention to detailing is decisive for avoiding, for example, black stripes under round windows and moss on garden walls. It always boils down to avoiding water concentrations on the facade.
5: No reinforcement, no expansion joint
If stress concentrations (tensile loads) occur in the design, it is advisable to provide additional reinforcement. Otherwise, you can get cracks in the facade. Even though brick is a very dimensionally stable masonry block, in projects with long walls (12 to 18 m) you must still provide expansion joints to avoid cracks. Other measures are also possible, such as installing masonry reinforcement.
Sudden expansion joints or masonry reinforcement may also be required in the event of sudden changes in the construction of the facade (for example, a large long sliding window above which the masonry continues).
6: Inadequate protection of fresh masonry
Because fresh masonry is particularly sensitive to excessive local water load, it is an absolute must to protect the new brick facade from rainwater. Otherwise, you increase the risk of leaching and efflorescence, but also of the mortar raining out.
7: Not respecting the connection
Not respecting the masonry bonds (half-brick, block, pile bond …) can result in so-called ‘dancing joints’ or joints that are not nicely placed one above the other. Some dressings – such as the bandage – require just this irregularity and so the joints may not be nicely aligned here.
8: Not scratching out the masonry
Scrape out fresh masonry for better grouting afterward. Respect the depth of the joint – best 1.5 times the thickness and at least 1 cm – and also avoid depth differences in the joint.
9: Joint thickness too small
The thickness of the joint must be adapted to the product. It is therefore important that you respect the minimum joint thickness for both the ribbon joints and the end joints. That way you can avoid problems like poor adhesion.
If you opt for thin joints, you must use suitable products such as adhesive mortars and thin mortars. Certainly, even with gluing and thin-walling, a minimum joint width is still required to accommodate tolerances on the dimensions of the bricks.
These tolerances are indicated on the technical datasheets of the facing bricks. Determine the ribbon joint thickness in advance by laying out a dozen bricks in a semi-brick bond. Measure the total height, divide by 10, and add the average joint thickness. This is how you obtain the layer size that you have to stake out on the masonry profiles.
Decision
Many feel called to brick their house themselves, but do not consider the possible consequences of inaccurate work. Therefore, it is important not only to choose quality materials but also to take into account all processing instructions of the manufacturer. You can build a wall yourself, but only if you do so according to the rules of good craftsmanship.